Nano Microporous Plate-Standard
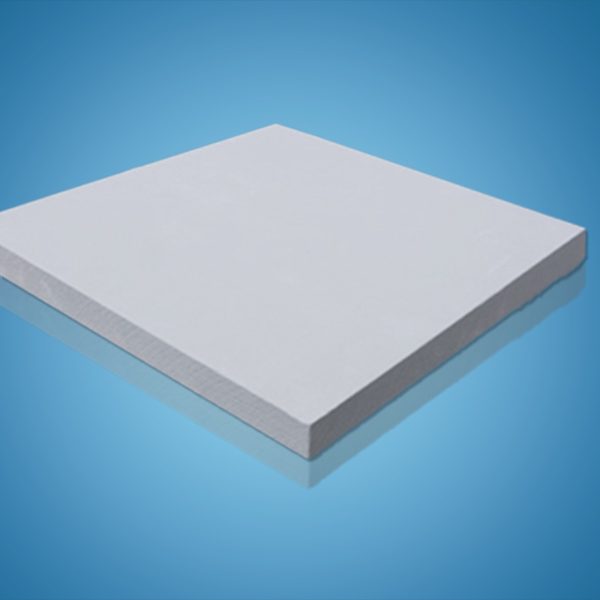
Product Description:
Anchor-Tech microporous insulation material is a high-performance thermal insulation product based on nanometer microporous principles. It is primarily composed of nanometer-scale Ti₂Si₂O₅ and silica particles, forming a microporous structure through a specialized process. This structure provides excellent high-temperature insulation, with thermal conductivity as low as that of still air.
The product range includes rigid boards, flexible sheets, and custom-shaped components, supporting tailored cutting, drilling, and complex curved surface fitting. It remains stable within a wide temperature range of -200°C to 1200°C, with thermal conductivity only 1/3 to 1/10 of conventional materials.
This lightweight and easy-to-process material can be customized into various shapes, making it suitable for high-temperature equipment in steel metallurgy, petrochemicals, glass production, and other energy-intensive industries, such as ladles, hot air ducts, and kilns. It significantly reduces heat loss and enhances equipment efficiency. The lightweight design minimizes the thickness and weight of the insulation layer, contributing to equipment downsizing and energy optimization while complying with environmental and non-toxic standards, providing a safe and efficient solution for high-temperature applications.
Insulation Mechanism
Anchor-Tech nanometer microporous insulation material achieves high-efficiency thermal insulation through three mechanisms:
- Suppressing gas heat transfer: With over 90% porosity, the nanometer-scale micropores (pore size < 90nm) are smaller than the mean free path of air molecules, blocking gas molecule collisions and convection, significantly reducing gas conduction heat loss.
- Extending solid heat conduction paths: Ultra-fine particles form a spiral porous structure, increasing the length of heat conduction paths. According to Fourier’s Law, thermal conductivity decreases exponentially as the conduction path length increases.
- Blocking thermal radiation: Light-blocking particles, evenly dispersed and similar in size to infrared wavelengths, refract and scatter high-temperature thermal radiation. Combined with Stefan-Boltzmann’s Law, this significantly suppresses radiative heat transfer at temperatures above 100°C, achieving full-spectrum thermal barrier performance.
Thermal Conductivity Comparison Table (W/m·K)
Average Temperature (℃) | Insulating Brick | Rock Wool | Ceramic Fiber | Calcium Silicate Board | Still Air | microporous |
‘-100℃ | 0.1180 | 0.0320 | 0.0300 | 0.0380 | 0.0160 | 0.0200 |
0℃ | 0.1200 | 0.0330 | 0.0320 | 0.0400 | 0.0180 | 0.0210 |
100℃ | 0.1220 | 0.0370 | 0.0360 | 0.0460 | 0.0200 | 0.0220 |
200℃ | 0.1250 | 0.0550 | 0.0440 | 0.0550 | 0.0220 | 0.0230 |
300℃ | 0.1300 | 0.0800 | 0.0600 | 0.0650 | 0.0250 | 0.0240 |
400℃ | 0.1350 | 0.1200 | 0.0800 | 0.0800 | 0.0360 | 0.0260 |
500℃ | 0.1440 | 0.1800 | 0.1100 | 0.0960 | 0.0440 | 0.0280 |
600℃ | 0.1600 | 0.1600 | 0.1200 | 0.0600 | 0.0300 |
Thermal Conductivity Comparison (W/m·K)
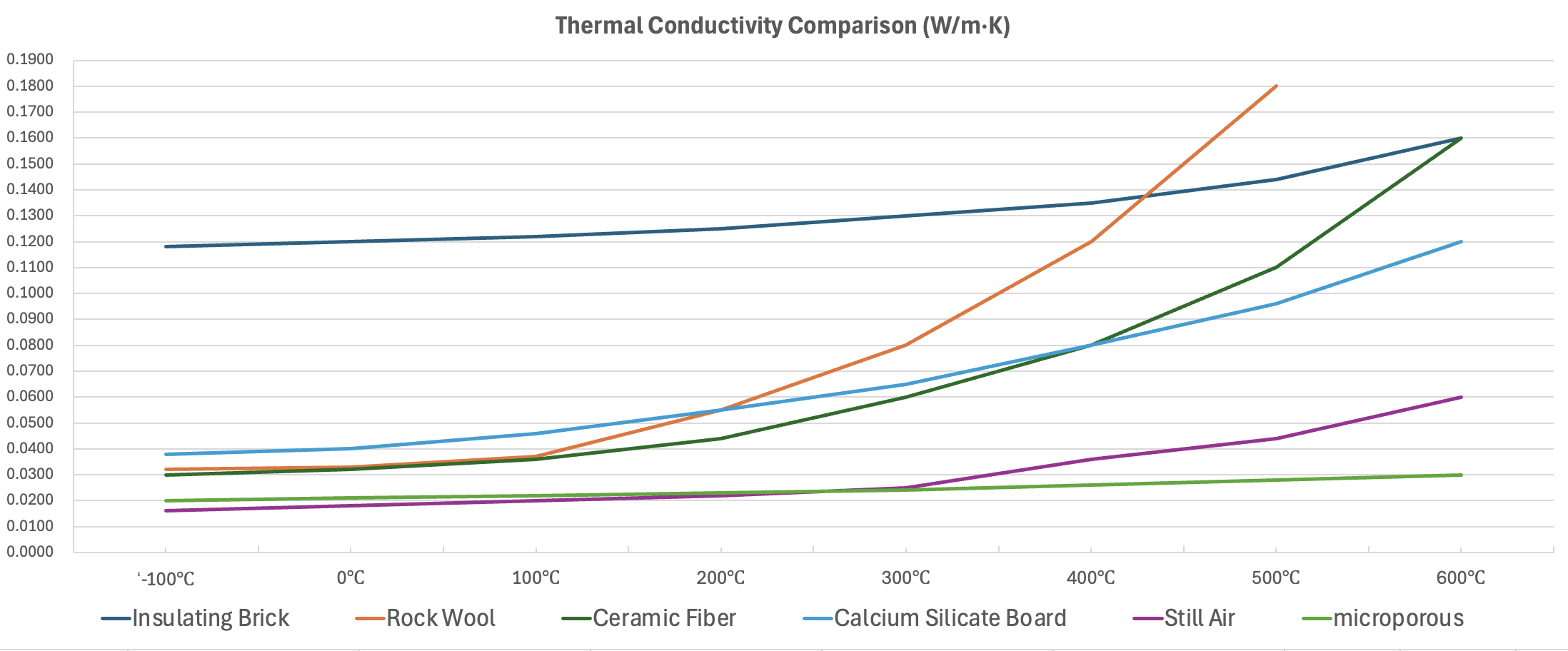
Thermal conductivity (W/mK)
200℃ | 0.022 |
400℃ | 0.024 |
600℃ | 0.028 |
800℃ | 0.034 |
Typical Application:
- Aluminium melting furnace
- Aluminum holding furnace
- Glass furnace
- Tempering furnace
- Roller hearth kiln
- Tunnel kiln
- Pit furnace
- Heat treatment furnace
- Cracking furnace
- Lifesaving capsule
- Electric heater
Specifications:
Product Model | Classification Temp (℃) | Density (kg/m³) | Linear Shrinkage at 800℃ | Chemical Composition | |
AMS12 | 1200 | 220-350 | <2% | SiO2 | 45% |
Ti2Si2O5+Al2O3 | 50% | ||||
AMS10 | 1000 | 220-350 | <2% | SiO2 | 50% |
Ti2Si2O5+Al2O3 | 45% | ||||
AMS09 | 900 | 220-350 | <2% | SiO2 | 45% |
Ti2Si2O5+Al2O3 | 45% | ||||
Standard Size(mm):1000*615*10,15,20,25,30,50 |
Product advantages:
✅ Ultra-low thermal conductivity for high efficiency and energy savings
- Thermal conductivity is only 1/3 to 1/10 of traditional materials.
- Reduces heat loss by 50%–75%, significantly lowering industrial equipment energy consumption.
- Ladle heat loss can be reduced to 0.3℃/min, and hot blast furnace efficiency increased by over 10%, reducing heat storage and shortening heating time by 20%–50%.
✅ Thin and space-saving, optimizing equipment design
- Provides the same insulation effect at only 1/4 to 1/6 the thickness of conventional materials.
- With a density of 220-350kg/m³, it is lightweight and space-efficient.
- Expands ladle capacity, reduces pipeline outer diameter, and is ideal for narrow spaces.
- When used in torpedo ladle inner walls, capacity increases by 5%, achieving both miniaturization and high efficiency.
✅ Wide temperature stability and high heat resistance
- Operates stably from -200℃ to 1200℃, with a linear shrinkage rate < 2%.
- Maintains structural stability in extreme conditions like RH dehydrogenation units and walking beam furnace water-cooled columns.
- Avoids sharp increases in thermal conductivity under high temperatures, ensuring long-term operational safety.
✅ Environmentally friendly and fiber-free, ensuring safety and health
- Non-fibrous, with no inhalation risks.
- Asbestos-free, certified by international health organizations.
- No dust pollution during installation and use, improving the working environment.
- Meets global low-carbon and environmental protection standards.
✅ Superior mechanical properties for easy processing and installation
- Can be cut, drilled, and bonded, adapting to complex structures.
- Customizable into special-shaped parts and flexible sheets, making it ideal for pipes and curved surfaces (e.g., engine covers and kiln corners).
- Increases installation efficiency by over 30%.
✅ Excellent thermal shock resistance and long service life
- Low specific heat capacity and high porosity, resistant to sudden temperature changes.
- In ladles, tundishes, and other frequently started and stopped equipment, it effectively resists thermal shock damage.
- Extends service life by 20%–30% compared to traditional materials.
✅ Precise temperature control to improve product quality
- Minimizes temperature fluctuations, ensuring uniform heat transfer.
- Reduces temperature gradients in molten steel and glass, improving casting quality and yield.
- In tundishes, after application, molten steel temperature fluctuations remain within ±5℃, significantly improving continuous casting quality.
✅ Recyclable and cost-effective
- Reusable material with long-term cost benefits.
- Although the initial investment is 10%–15% higher than traditional materials, it reduces overall costs by 30% within three years through energy savings and extended equipment lifespan.
- Supports sustainable industrial development.
✅ Superior water resistance
- Optional hydrophobic version effectively resists moisture penetration, extending material lifespan in humid environments.